Fountain Solutions for offset printing
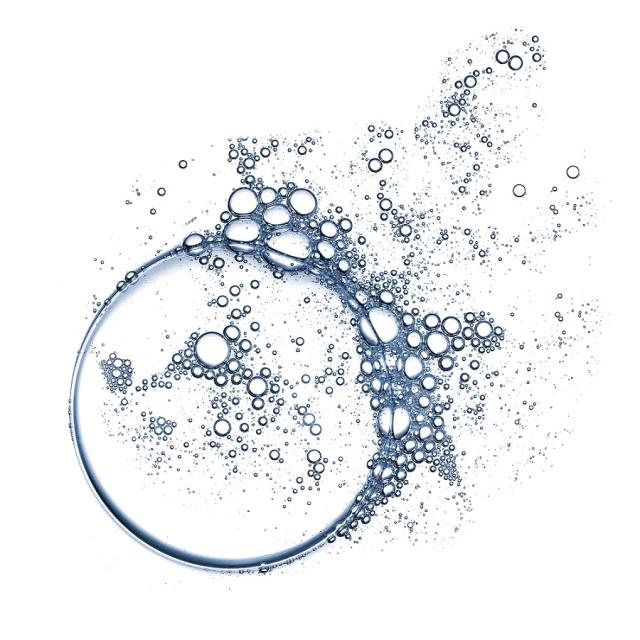
Foam formation is a common issue in fountain solutions due to the agitation and aeration that occurs during the printing process.
Foam is created when air becomes trapped within the solution and forms a layer of bubbles on the surface.
Foam can cause several problems in offset printing, such as reduced ink transfer, uneven ink distribution, dot gain, ink emulsification, and poor print quality.
It can also lead to equipment malfunctions, such as blockages in the dampening system or plate clogging.
The main functions and benefits of defoamers in fountain solutions for offset printing are as follows:
- Foam Prevention: Defoamers are added to fountain solutions to prevent foam formation right from the start. By reducing the surface tension of the solution, defoamers minimize the likelihood of air entrapment and bubble formation during the printing process.
- Foam Suppression: In cases where foam is already present in the fountain solution, defoamers are used to quickly suppress and eliminate it. They break down the foam bubbles and prevent them from interfering with the printing process.
- Enhanced Ink Transfer: Foam in the fountain solution can hinder the proper transfer of ink from the plate to the paper. Defoamers help to ensure smooth ink flow, allowing for consistent and accurate ink transfer onto the printing surface. This results in improved print quality, sharpness, and color fidelity.
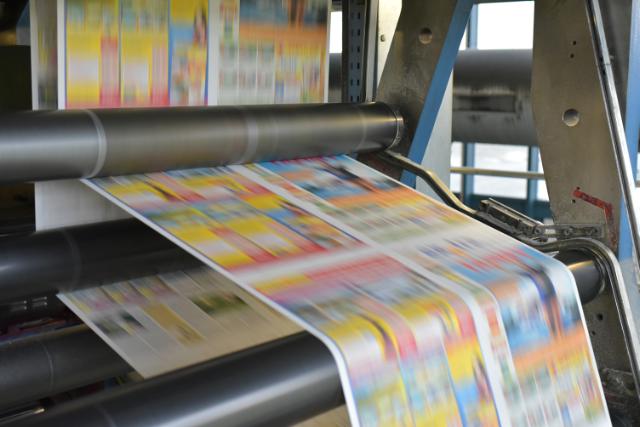
Get in touch about information and samples
We make it simple and hassle-free! We're here to provide the best possible customer service!
Just let us know what you need, and we will ensure fast and reliable delivery.
Don’t hesitate to reach out! Contact us here
Need expert advice ?
Whether you have questions about specific products, formulations, or specialized services, we’re ready to advice you through the process.
Feel free to reach out with any inquiries or special requests.
Contact one of our experts here
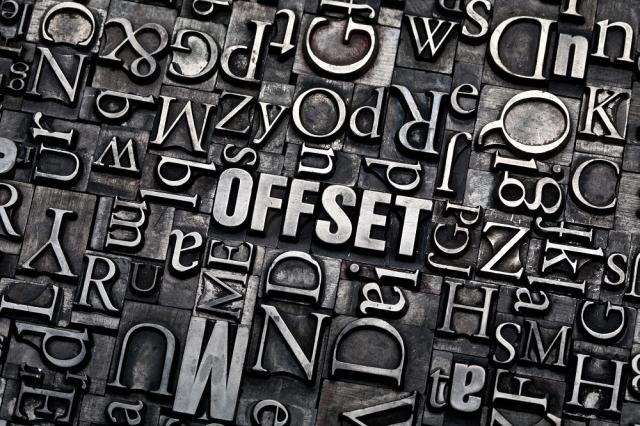
- Stable Dampening System: The dampening system in offset printing requires a consistent and stable supply of fountain solution.Excessive foam can disrupt the balance and consistency of the solution, leading to variations in ink-water balance and overall print quality. Defoamers maintain a stable dampening system by preventing foam-related fluctuations.
- Reduced Downtime and Maintenance: Foam-related issues can cause frequent interruptions, equipment downtime, and increased maintenance requirements. By incorporating defoamers into the fountain solution, printers can minimize foam-related problems, ensuring continuous production and reducing the need for equipment cleaning and repairs.
- Cost Efficiency: Foam-related problems, such as ink waste, rejections, and production delays, can be costly for printing operations. Defoamers help to optimize the printing process, minimize ink and substrate wastage, and reduce the overall production costs.
ESTI CHEMs product DEFOAMER 1000 has established itself as a superior defoamer for application in fountain solution concentrates. It fulfills the requirements listed above.
Learn more:
Learn more
Four reasons to do business with us
More than 30 years of experience
ESTI CHEM has more than 30 years of experience in the development of sustainable products based on natural raw materials.
We help customers transforming their products to fit the needs of the future.
Short time delivery and a reliable supply chain
ESTI CHEM knows the importance of timely access to raw materials.
A broad range of our products are available from stock, and our supply chain team is ready to assist you.
We deliver samples, technical information & support
Development of new formulations can be a bumpy road with many challenges on the way.
ESTI CHEM will assist you with product samples, technical information & support during the development process
Certified ISO 9001 - 14001 – 45001 – RSPO – Rated ECOVADIS Platinum
ESTI CHEM is certified according to ISO 9001, 14001, 45001, and RSPO.
We are Platinum-rated by Ecovadis on sustainability.
Our processes are well-documented and focused on providing service and support to our customers.
Get in touch
We appreciate your interest in our products and services.
Let us get back to you
Use the contact form and we will strive to make a reply in 24hours.
